
- #DELTA ORCAVIEW DIFFERENTIAL PRESSURE PID LOOP UPDATE#
- #DELTA ORCAVIEW DIFFERENTIAL PRESSURE PID LOOP MANUAL#
- #DELTA ORCAVIEW DIFFERENTIAL PRESSURE PID LOOP FULL#
- #DELTA ORCAVIEW DIFFERENTIAL PRESSURE PID LOOP SIMULATOR#
Shorten installation times by eliminating complex wired infrastructures, and lower overall implementation costs of process measurement, with ABB wireless devices featuring WirelessHART communications – Measurement made easy.
#DELTA ORCAVIEW DIFFERENTIAL PRESSURE PID LOOP UPDATE#
The 266 WirelessHART Pressure Transmitters have a battery life of about 10 years at 32 sec update rates, delivering a very cost-effective and reliable solution to monitor your process assets. You can now monitor hard-to-reach locations and keep your employees out of dangerous and hazardous areas. This certification is a real guarantee of protection and makes of 266DSH the smartest fit in Safety-critical loops.Ģ66DSH features WirelessHART communication protocol allowing the addition of pressure measurement points throughout your operation. SIL2/SI元 certification issued by TÜV Nord according to IEC 61508 represents another key-feature within 266 pressure transmitter portfolio. In addition, 266DSH features Plugged Impulse Line Detection as standard helping customer in detecting when the impulse line are going to be plugged. Moreover, the innovative TTG (Through The Glass) technology allow users to configure the instruments in the field without removing the windowed front cover and consequently to save a lot of time setting all parameters by using the finger tips in few minutes. Its intuitive plug-and-play display with easy setup procedure really helps users by saving time and lowering maintenance and inventory costs. Plt.This transmitter features in-field replaceable electronics module that thanks to the auto-configuration functionality dramatically improves plant productivity.
#DELTA ORCAVIEW DIFFERENTIAL PRESSURE PID LOOP SIMULATOR#
And also the PID Simulator page to use a live PID Simulator. See post WHAT IS A PID CONTROLLER for a basic example of a PID controller. plot (t ,pv, 'b-' ,linewidth = 3 ,label = 'Process Variable (PV)' ) A PID (Proportional Integral Derivative) controller works by controlling an output to bring a process value to a desired set point. plot (t ,sp, 'k-' ,linewidth = 2 ,label = 'Set Point (SP)' ) Y = odeint (process ,pv, ,args = (op ,Kp ,taup ) )ĭef plot_response (n ,mode ,t ,pv ,op ,sp ): Ie = ie - e * delta_t # anti-reset windup If i >= 1: # calculate starting on second cycle zeros (ns+ 1 ) # integral of the errorĭpv = np. Include a plot of the integral of the error between the set point ( SP) and process variable ( PV) with anti-reset windup. Simulate the response of a PI controller with `\tau_I=200`. What happens with increased `K_c` in terms of offset and oscillation? Include a plot of the error between the set point ( SP) and process variable ( PV). Implement a set point change from 0 to 10 and back in automatic mode (closed-loop).
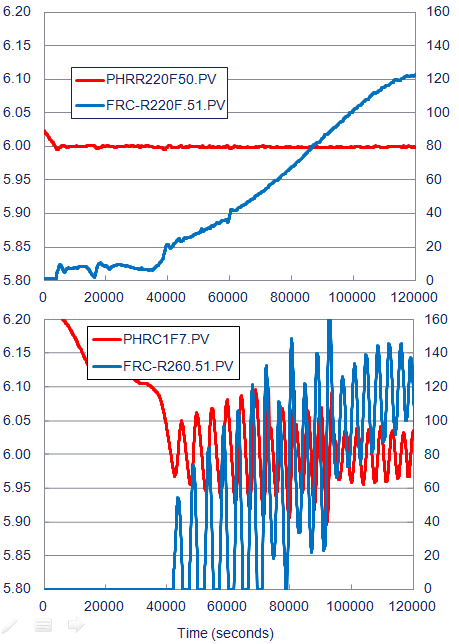
With the dead time, simulate the response of a P-only controller with `K_c=2` and `K_c=0.5`. Explain what happens in terms of oscillations.
#DELTA ORCAVIEW DIFFERENTIAL PRESSURE PID LOOP MANUAL#
Simulate the behavior for making a step change in manual mode from 0 to 10 (and back). Explain what happens and why.Īdd dead time `\theta_p=100` as an input delay.
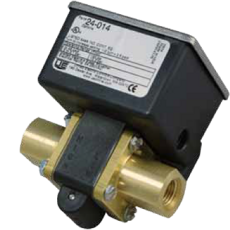
Simulate the PI controller response with integral reset times `\tau_I=200, 100, 10`. What happens with increased `K_c` in terms of offset and oscillation?Ĭonfigure the controller to add an integral term in addition to the proportional control with `K_c = 2`. Simulate the behavior for using a P-only controller with `K_c = 2` and `K_c=0.5`. Explain what happens in terms of oscillations or a smooth response.
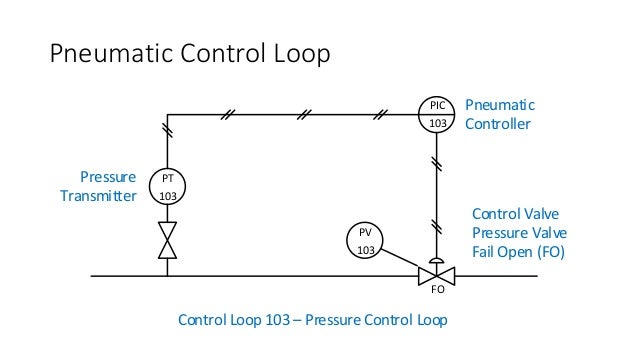
The value of the controller output `u(t)` is fed into the system as the manipulated variable input.
#DELTA ORCAVIEW DIFFERENTIAL PRESSURE PID LOOP FULL#
The PI controller is the most popular variation, even more than full PID controllers. There are some related problems, such as lack of control over BHP, longer working. However, at the present stage, BHP control still focuses on conventional PID control and simple intelligent control, requiring repeated data alignment. A variation of Proportional Integral Derivative (PID) control is to use only the proportional and integral terms as PI control. The bottom hole pressure (BHP) of managed pressure drilling (MPD) is a typically unstable object with hysteresis that is difficult to be directly controlled.
